cartridge filters
cartridge filters
LiandaFiltration’s new cartridge filter housing is designed for industrial and sanitary applications. The housing is made of 316L sanitary stainless steel with a mirror-polished inner surface. It is compatible with a variety of liquid cartridge filter element interfaces and has both high flow processing and ultra-fine particle interception capabilities. Whether it is a clean cartridge filter for food and beverage production lines or a corrosion-resistant cartridge filter housing in chemical processes, LiandaFiltration can provide stable and reliable filtration solutions.
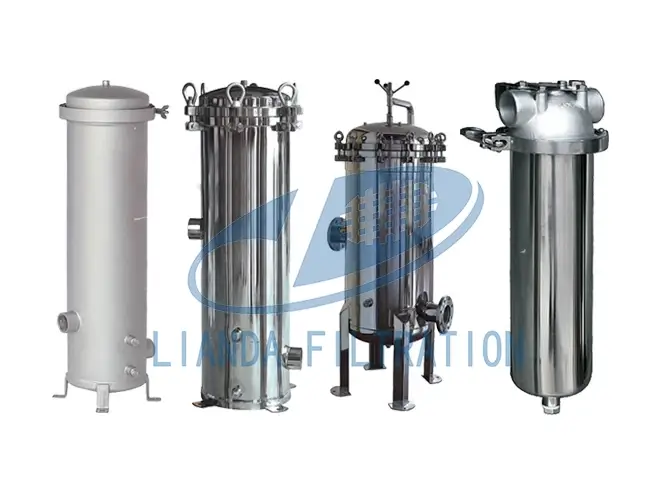
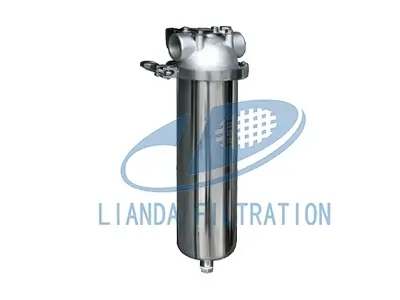
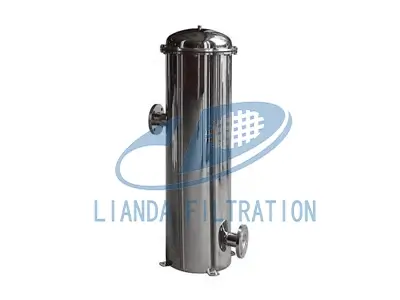
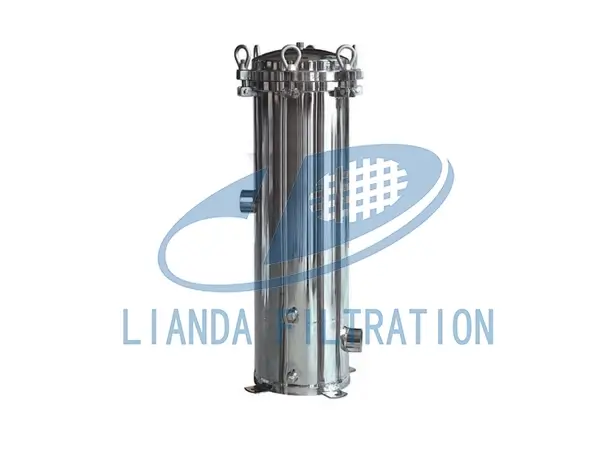
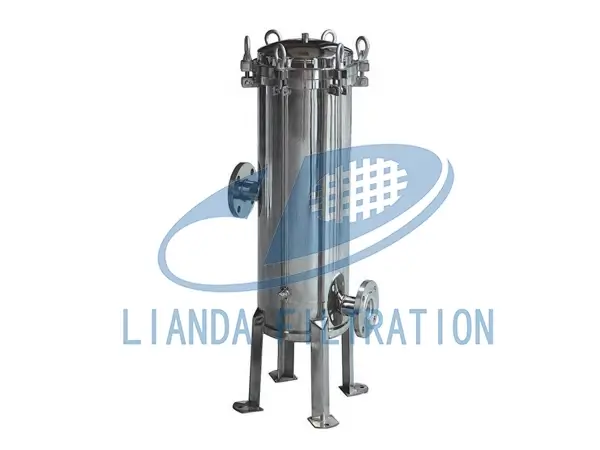
parameter term | Specification range |
material | 304 / 316L Sanitary Stainless Steel |
Cartridge type | Folded cartridge, sintered cartridge, PP cartridge |
Filtration accuracy | 0.5 µm, 1 µm, 5 µm, 10 µm, 20 µm (customizable) |
Maximum working pressure | 10 bar (145 psi) |
Maximum working temperature | 150 ℃ |
Interface form | Tri-Clamp Quick Release, Flange (DIN, ANSI, JIS), Threaded Connection |
capacity | 5″, 10″, 20″, 30″ Standard cylinder length (can be customized) |
surface treatment | Mirror polished inside and outside, Ra ≤ 0.4 µm |
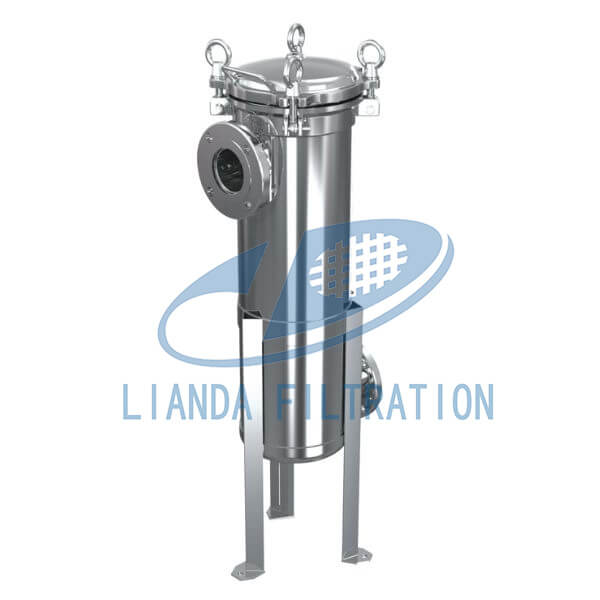
High sealing reliability
- Use “O-ring” or “metal gasket” double sealing design to prevent bypass;
- Housing flange or quick-release clamp installation, good sealing and quick replacement.
High temperature and corrosion resistance
- Metal filter element can withstand temperatures of 200-600℃, PTFE/ceramic can withstand higher temperatures;
- The surface is passivated or coated, resistant to chemical media erosion, and has a long service life.
Modular cartridge structure
- The filter element is arranged in a cylindrical shape, stacked and sealed, with a large filtration area and compact volume;
- The number of filter elements can be flexibly increased or decreased according to flow requirements, and it has strong scalability.
High-efficiency filtration performance
- Uniform micron pore size and high interception efficiency;
- Gradient filtration design effectively extends the life of the filter element and reduces the pressure difference.
Food and Beverages
Pre-filtration and sterile filtration of juice, beer, and dairy products to ensure taste and food safety.
Pharmaceutical Biology
Terminal filtration of water for injection and buffer to meet GMP and FDA aseptic production specifications.
Chemical Coatings
Decolorization and impurity removal of solvents, resins, coatings, and cleaning fluids to prevent clogging of downstream equipment.
Electronic Semiconductors
Ultrapure water systems and chemical liquid filtration to eliminate dust and ion pollution.
Petroleum and Petrochemicals
Online circulation filtration of lubricating oil and hydraulic oil to extend equipment life and reduce maintenance costs.
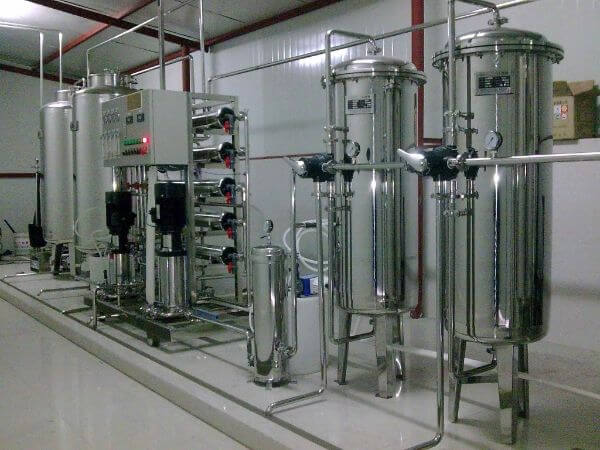
FAQ
According to the system design flow rate (m³/h), required filtration accuracy and maximum pressure difference, select the corresponding cylinder length and number of filter elements. If professional calculation is required, please provide the medium viscosity, temperature and flow rate, and we will provide a dedicated selection report.
316L sintered filter elements can withstand high-temperature sterilization at 150°C, and their performance remains stable after multiple steam or hot water flushings. PP filter elements are recommended to be used at the temperature specified by the manufacturer.
It is recommended to replace the filter element when ΔP exceeds 0.2 bar or the output drops by 20%, generally every 3-6 months, depending on the operating conditions.
It supports customization of interface, tube length, material, label and pressure level to meet special working conditions and OEM/ODM requirements.
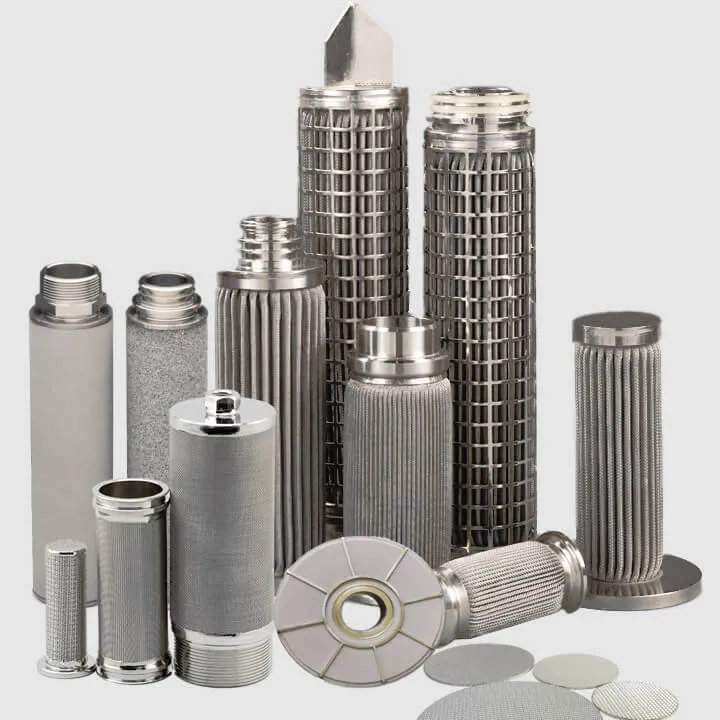
Sintered filter element

Mesh Demister

Wire Mesh Packing
