Sintered Metal Fiber Felt
Sintered Metal Fiber Felt
Sinter metal fiber felt filter is made of overseas stainless steel fiber as raw material, and it is a high porosity porous deep filtration material with process of non-spinning, folding of the metal fiber.
Sintered metal fiber felt Cartridge (XKF) original uses imported stainless steel fiber as raw material. After non-woven laying and lamination of metal fiber, it is made into porous deep filter material by high-temperature vacuum sintering. Its most prominent feature is high porosity. Since the diameter of the metal fiber is very uniform, the pore size distribution is limited to a very narrow range, and the metal fiber felt provides good gas permeability while ensuring filtration precision. The metal fibers also increase the filtration area by folding, thereby increasing the amount of filter dirt.
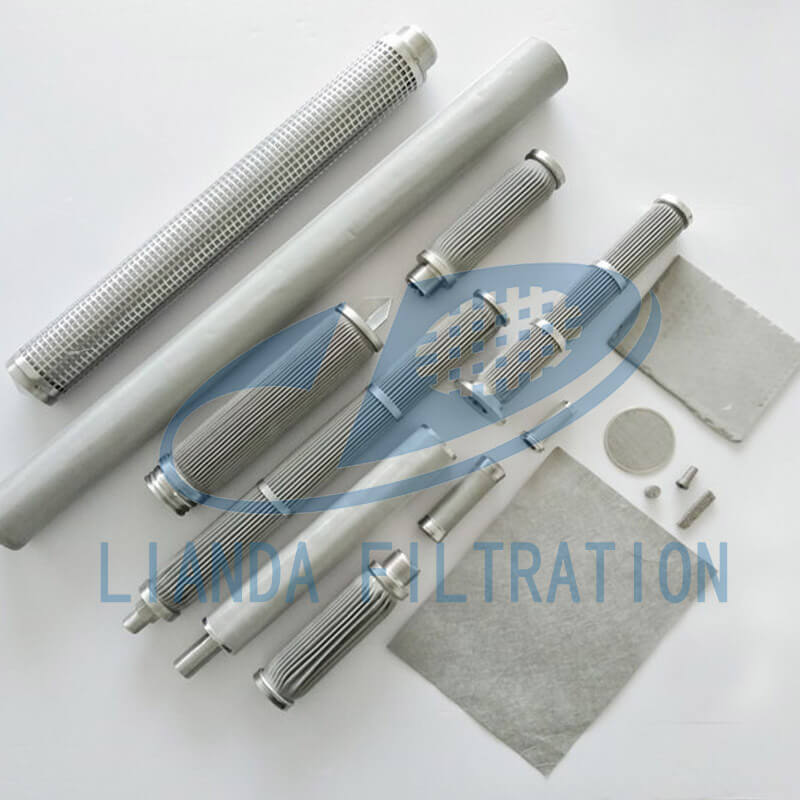
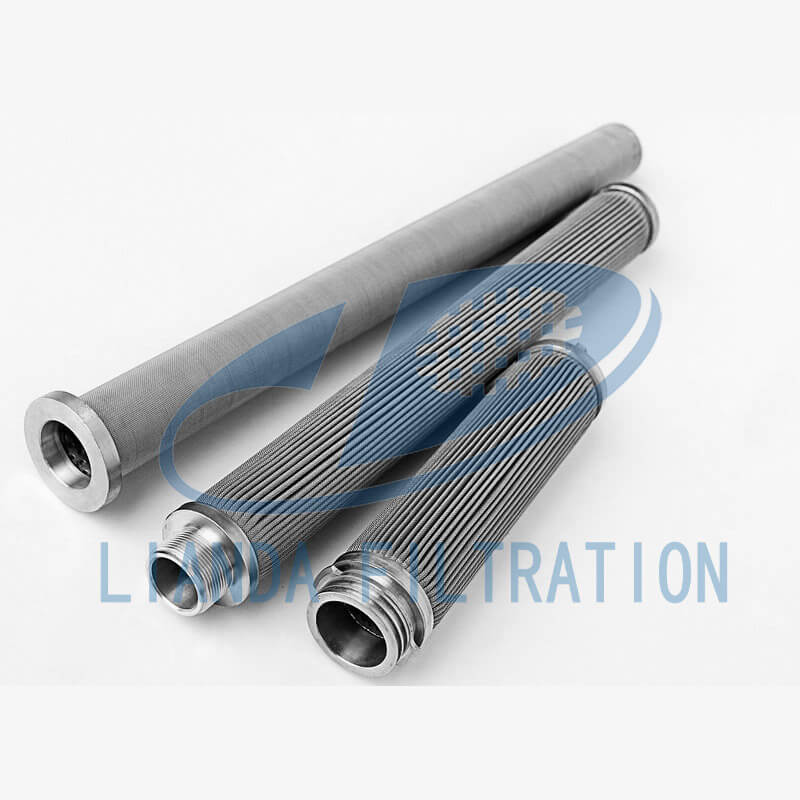
Technical parameters
绝对评分 微米 | 起泡点压力 (Pa) ±8% | 平均透气性 升/分量米/分钟 | 厚度 毫米 | 重量 克/米2 | 孔隙 度 % | 纳污能力 毫克/厘米2 |
3 | 12300 | 9 | 0.35 | 975 | 65 | 6.40 |
5 | 7600 | 34 | 0.34 | 600 | 78 | 5.47 |
7 | 5045 | 57 | 0.27 | 600 | 72 | 6.47 |
10 | 3700 | 100 | 0.32 | 600 | 77 | 7.56 |
15 | 2470 | 175 | 0.37 | 600 | 80 | 7.92 |
20 | 1850 | 255 | 0.49 | 750 | 81 | 12.44 |
25 | 1480 | 320 | 0.61 | 1050 | 79 | 19.38 |
30 | 1235 | 455 | 0.63 | 1050 | 79 | 23.07 |
40 | 925 | 580 | 0.66 | 1200 | 77 | 25.96 |
60 | 630 | 1000 | 0.70 | 750 | 87 | 33.97 |
Note: The above parameters can be optimized and customized according to working conditions.
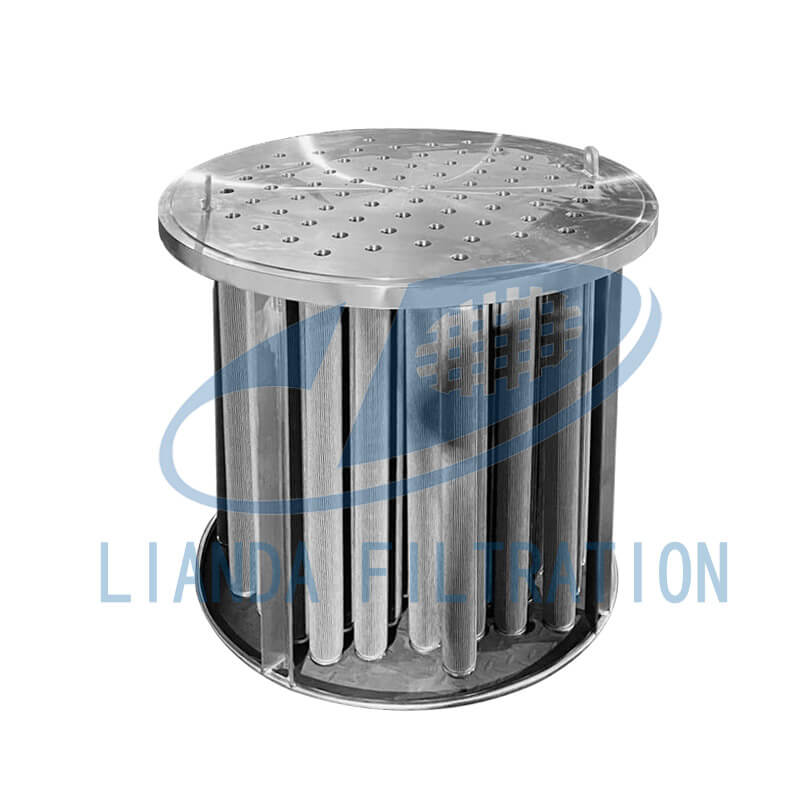
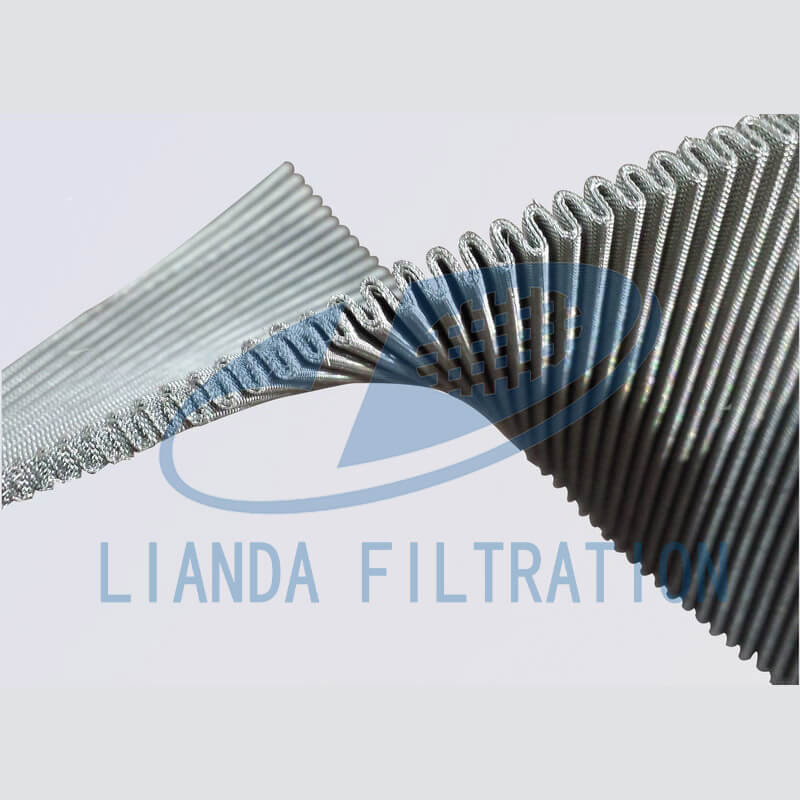
Product Features and Benefits
Deep filtration and high retention
The sintered fiber felt structure forms a progressive pore size gradient, achieving deep capture of tiny particles, with a filtration efficiency of up to 99.9%, making it a true stainless steel sintered fiber filter.
Large specific surface area and low pressure drop
The felt-like fiber network provides a large specific surface area, which keeps the pressure drop to a minimum while maintaining high flux, reducing energy consumption.
Excellent mechanical strength
The metal fiber has outstanding strength after sintering, and is resistant to multiple cycles of pulse cleaning and backwashing, with a lifespan far exceeding that of traditional filter membranes and ceramic filter elements.
High temperature and chemical resistance
The 316L material can work stably at 550°C and in strong acid and alkali environments, and is suitable for harsh chemical and high-temperature gas filtration applications.
Cleanable and regenerable
Supports high-pressure water, steam, chemical solvents or ultrasonic cleaning, and the performance recovers quickly after cleaning, significantly reducing long-term operating costs.
Product application industry
Chemical and petrochemical: catalyst protection, reactor tail gas particulate filtration, solvent recovery pre-filtration
Pharmaceutical and biological: fermentation gas purification, pharmaceutical steam fine filtration, sterile air terminal filtration
Environmental protection and industrial waste gas: desulfurization and denitrification tower tail gas dust removal, VOCs recovery device front-end capture
Energy and power: turbine air purification, lubricating oil impurity removal, high-temperature gas filtration
Food and beverage: hot oil fine filtration, beverage clarification, oil decolorization pre-treatment
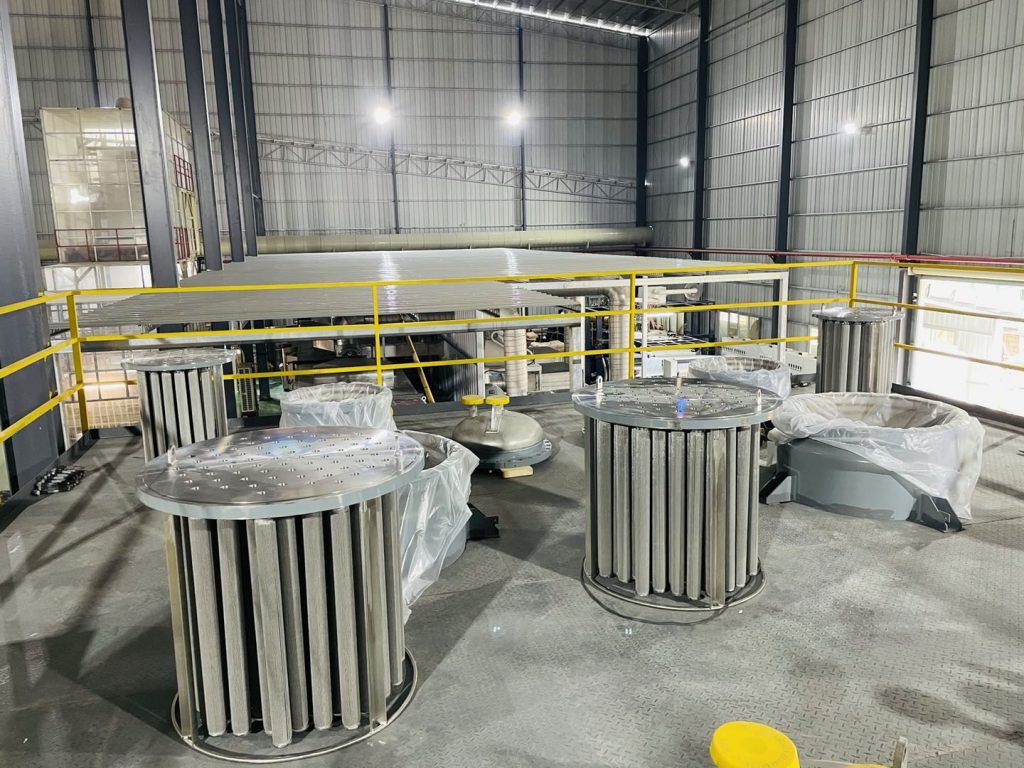
How do we produce your sintered filters and perform quality control?
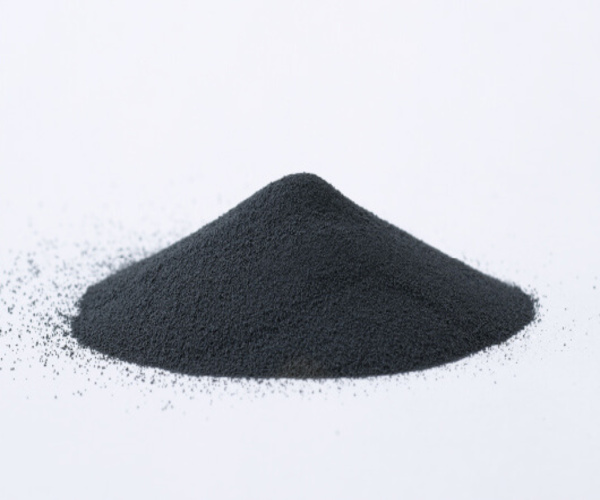
raw material
LianDaFiltration always insists on selecting uniform raw material powder to produce each sintered filter with large pore size, high tensile strength and temperature stability in the future.
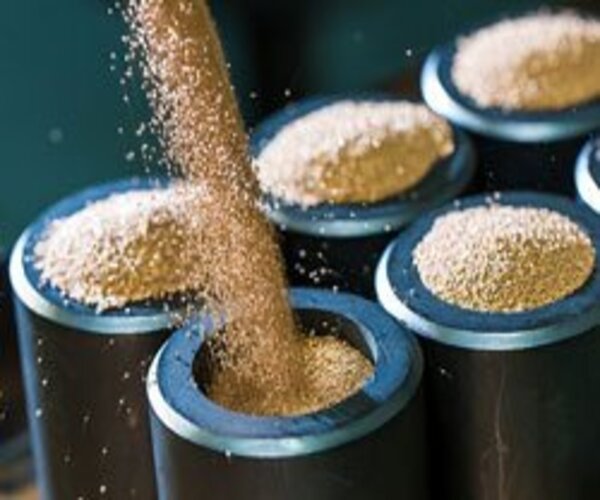
powder filling
The isostatic pressing filling process is used to achieve uniform powder density and eliminate pore defects.
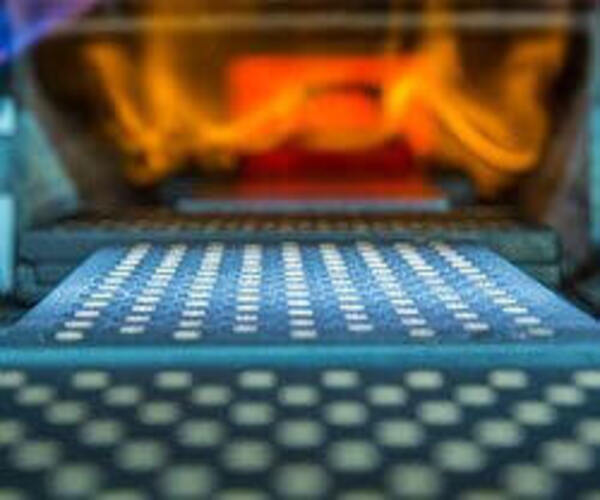
High sinterability
High temperature sintering under vacuum argon protection improves the tightness of micropore connection and enhances pressure resistance.
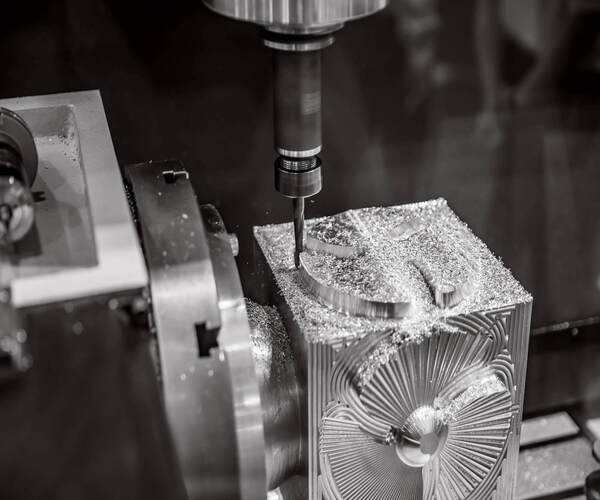
CNC machining
Through CNC turning and grinding, the filter element geometric accuracy is maintained at ±0.02 mm to meet high-precision filtration requirements.
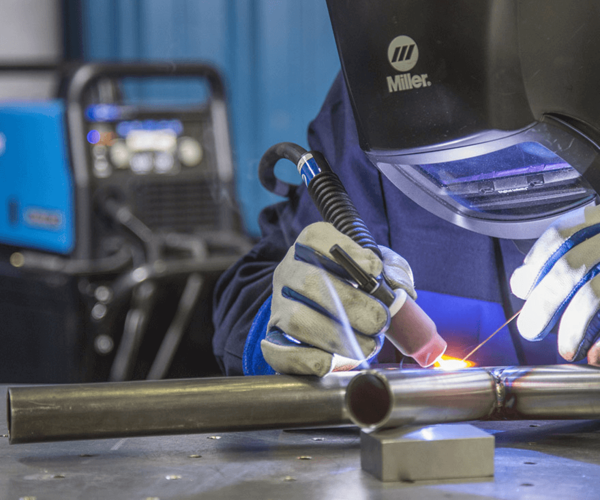
weld
The laser welded joints are delicate and smooth, with no risk of leakage, which improves the sealing reliability of the filter.
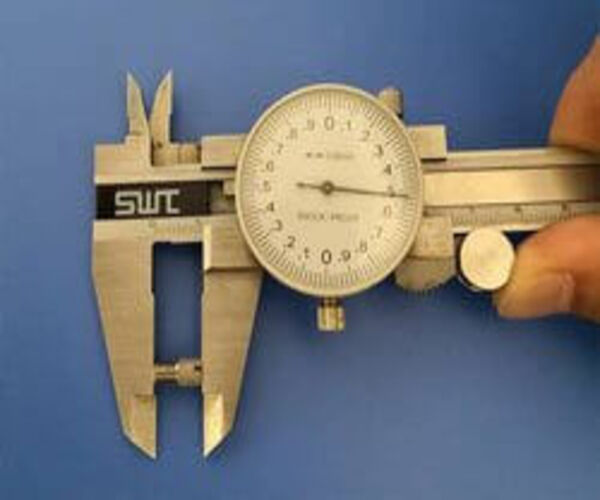
Dimensions
LianDaFiltrationCheck all dimensions of the sintered filter using pressure gauges and high-efficiency dimension monitoring equipment.
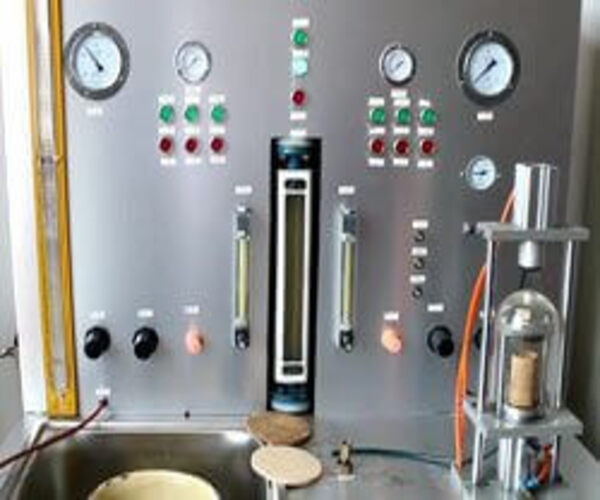
filter test
Micropore interception rate evaluation and pressure burst test are used to ensure that each filter element passes the quality inspection in one go.
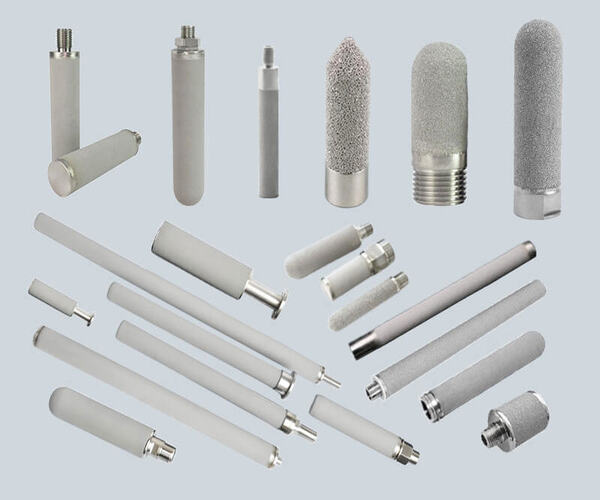
Product packaging
LianDaFiltration All sintered filter products and accessories are packed in accordance with international standard safety procedures to meet the standards,
Through the above eight processes and strict testing, LiandaFiltration provides you with stable and reliable sintered filter products.
FAQ
Determined by media particle size and downstream equipment requirements, generally 0.5–1 µm is used for high-precision filtration, and 3–5 µm is suitable for pre-filtration; LiandaFiltration can provide process selection guidance.
Standard 304/316L sintered metal fibers can withstand temperatures ≤550°C, but the pulse pressure should not exceed 4 bar to avoid fiber fatigue fracture.
The fiber felt has a more continuous pore structure, higher dust holding capacity, and more obvious gradient filtration, making it suitable for working conditions with high dust content, high temperature, or oil mist.
Yes. LiandaFiltration can customize the outer diameter, length, fiber diameter and material (such as Inconel, Hastelloy) according to customer needs to meet special working conditions.
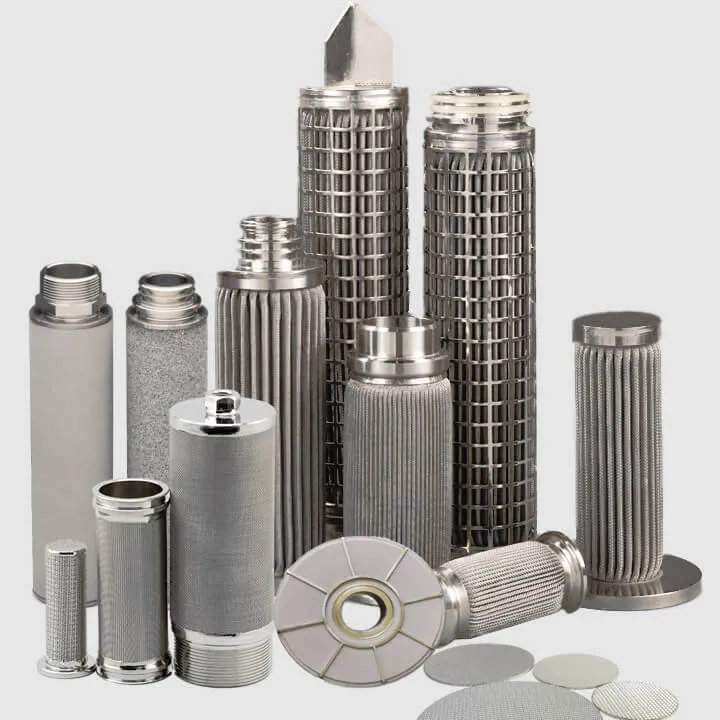
Sintered filter element

Mesh Demister

Wire Mesh Packing
