Fixed valve tray
Fixed valve tray
Fixed valve tray is an innovative tower internal that fixes the valve plate on the tray, also called V-Grid fixed valve tray. Different from the traditional floating valve tray, the fixed valve tray integrates the valve cover and valve leg by stamping or welding, which is not easy to get stuck or fall off, with a simple structure and low manufacturing cost. Its non-clogging valve plate design is particularly suitable for complex media with high viscosity, fiber or easy scaling, providing stable gas-liquid separation and mass transfer efficiency for distillation, absorption, extraction and other processes.
The solid valves on the tower plate are generally made by direct stamping, such as tongue-type guide solid valves, trapezoidal solid valves, etc. Although the structures of these solid valves are different, their main function is to prevent the rising gas under the tower plate from directly rushing vertically to the liquid flowing on the tower plate, but to make the rising gas pass through the solid valve and then disperse horizontally along the tower plate surface into the liquid to increase the gas-liquid contact time. Therefore, its tower plate efficiency is similar to that of the floating valve tower plate. Since the solid valve is afraid of pressure and stepping, it brings inconvenience to the installation and maintenance of the solid valve tower plate. The trapezoidal solid valve can solve this shortcoming, but it has no guiding function and its mass transfer efficiency is also low, which needs to be improved urgently.
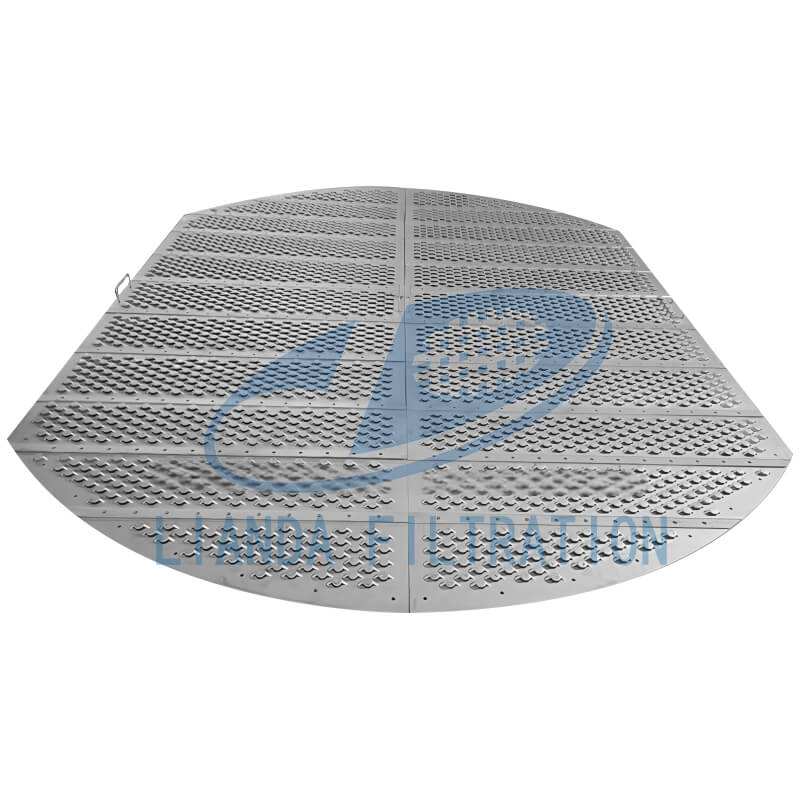
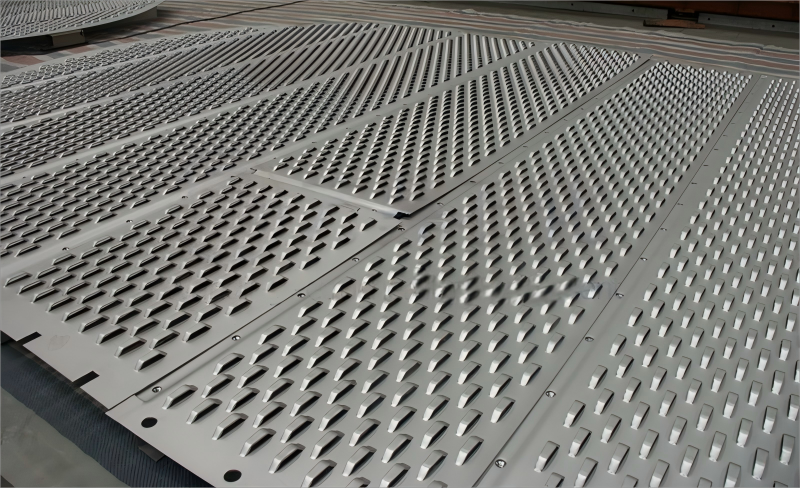
Technical parameters
parameter | Customizable range |
Material | 304 / 316L stainless steel; optional Inconel, Hastelloy |
Board diameter | φ600–φ2400 mm; non-standard customization is supported |
Opening ratio | 10–25% (adjustable) |
Valve plate height | 2–5 mm |
Bonnet shape | Trapezoidal / Semi-elliptical / Triangular / Cross |
Effective via | φ10–φ30 mm |
Mass transfer efficiency | Equivalent to 0.8–1.0 times of floating valve tray |
Pressure drop range | 50–200 Pa (depending on air velocity and load) |
operating temperature | –50°C to 350°C |
Installation method | Flange bolts / welding |
Note: The above parameters can be optimized and customized according to working conditions.
Product Features and Benefits
Compact structure, anti-stuck
The valve cover and valve legs on the solid valve tray are integrated, without floating parts, and will not be stuck due to vibration or viscous media.
Low manufacturing cost and easy processing
The stamping or laser cutting combined with welding process is used for one-time molding, which reduces mold and labor costs.
Non-blocking valve plate
There is no dead angle under the valve cover, and there are enough channels around the valve plate to cope with high viscosity and entrained solid conditions.
Good mass transfer efficiency
The horizontal blow-out airflow cooperates with the trapezoidal valve cover angle to reduce mist entrainment, extend the gas-liquid contact time, and the overall mass transfer efficiency is close to the floating valve tray.
Wide range of applications
It can be used in a variety of tower processes such as petrochemical distillation, gas absorption, liquid-liquid extraction, and separation of high-viscosity materials.
Valve-Tab Tray (Fixed Valve Tray) Structure:
Fixed valve trays offer a low-cost design that mimics the shape of conventional valves by stamping the valve directly from the tray deck. With no moving parts, they eliminate wear and sticking issues common to floating valves. Although their minimum operating turndown is somewhat limited compared to other valve trays, fixed valve trays boast a higher maximum turndown and greater throughput than sieve trays.
Valve sizes can be tailored to process conditions within the column, with typical heights of 60 mm, 30 mm, or 20 mm. Smaller valve dimensions yield lower entrainment and higher mass transfer efficiency; as the ratio of slot area to valve hole area decreases, both dry and wet tray pressure drops increase and weeping is reduced. Consequently, smaller valve sizes deliver higher capacity.
A key advantage of fixed valve trays is their resistance to fouling, making them ideal for applications involving slurry, fermentation broths, or wash columns where solids loading can cause blockages. Each fixed valve is formed as a semi-elliptical body stamped directly from the tray deck, projecting as a trapezoid on the tray surface. This geometry helps reduce liquid head gradients across the tray and minimizes back-mixing.
Product application industry
Petroleum refining: gas-liquid separation at the top of vacuum and atmospheric distillation towers;
Chemical synthesis: high viscosity reaction towers such as styrene polymerization and methanol synthesis;
Environmental desulfurization and denitrification: droplet separation in flue gas absorption towers;
Pharmaceuticals and biology: distribution of reflux liquid in fermentation tanks and uniform distribution of gas in towers;
Liquid-liquid extraction: phase interface distribution and mass transfer in solvent extraction towers.
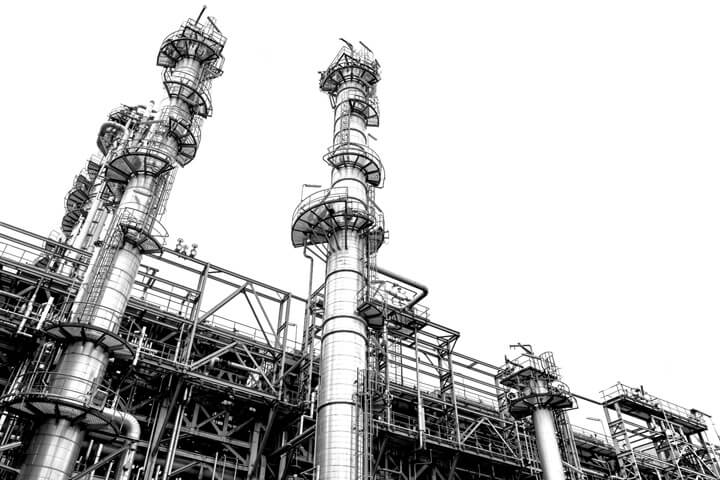
FAQ
The fixed valve tray has no moving parts and will not get stuck or fall off, making it more suitable for media with high viscosity and high solid content; the manufacturing and maintenance costs are lower.
It is fixed with flange bolts or welding, easy to disassemble and can be replaced on site without major maintenance.
Determined by gas velocity and load, a general opening rate of 15–20% can take into account both pressure drop and mass transfer efficiency. LiandaFiltration can provide professional selection guidance.
Yes. The size and bonnet shape can be customized according to the tower diameter, layout and interface form to achieve quick docking and installation.
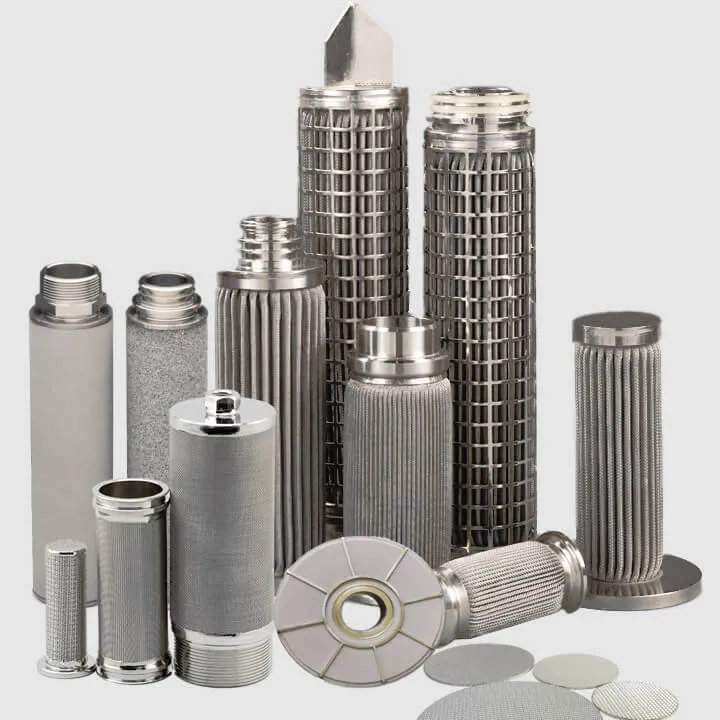
Sintered filter element

Mesh Demister

Wire Mesh Packing
