Float valve tray
Float valve tray
Since its introduction in the mid-20th century, the float valve tray has been known for its floating opening and automatic gas channel adjustment. Compared with traditional bubble cap trays, the float valve tray has greater operational flexibility, lower mist entrainment and higher mass transfer efficiency. We provide a variety of float valve tray series: disc type (F1/V1), HTV boat-shaped float valve tray, guided trapezoidal float valve tray, ADV differential float valve tray and economical fixed valve tray to meet different gas-liquid loads and process requirements.
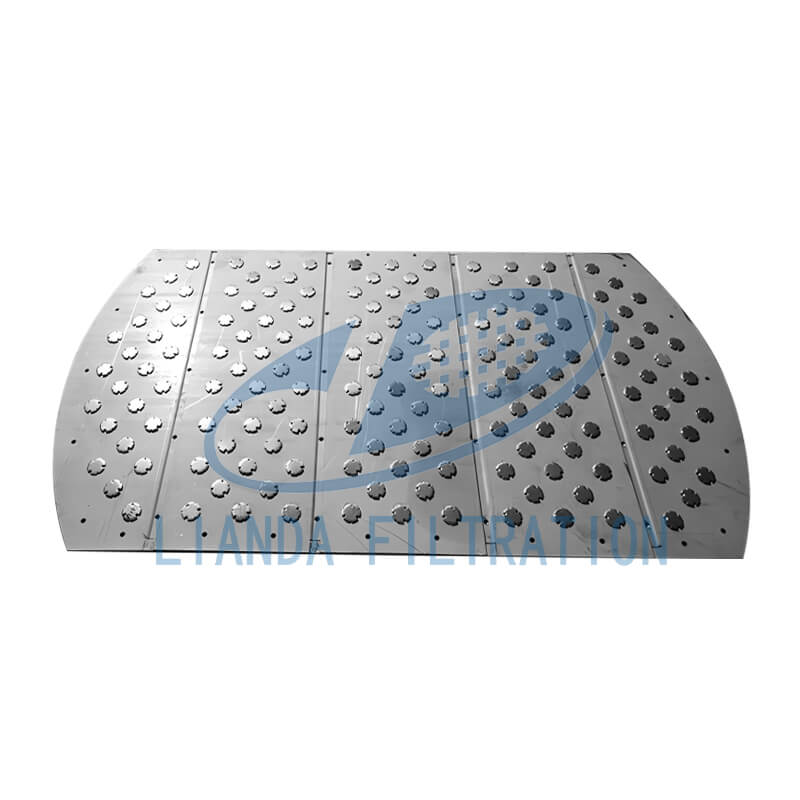
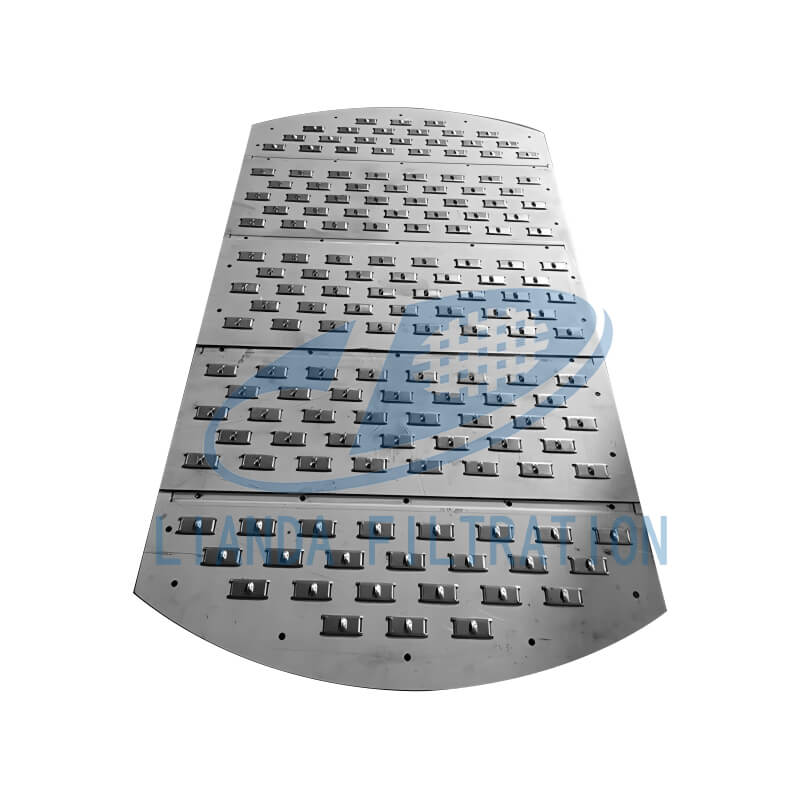
Technical parameters
type | Effective opening rate | Gas phase load range | Pressure drop range | Material | |
Disc type floating valve tray (F1/V1) | 10–15% | 0.05–0.30 m/s | 100–300 Pa | 304/316L SS | |
HTV ship-shaped floating valve tray | 12–18% | 0.08–0.40 m/s | 80–250 Pa | 316L SS | |
Guided trapezoidal valve tray | 12–20% | 0.05–0.45 m/s | 70–230 Pa | 316L SS | |
ADV differential valve tray | 14–22% | 0.10–0.50 m/s | 60–200 Pa | 316L SS | |
Note: The above parameters can be optimized and customized according to working conditions.
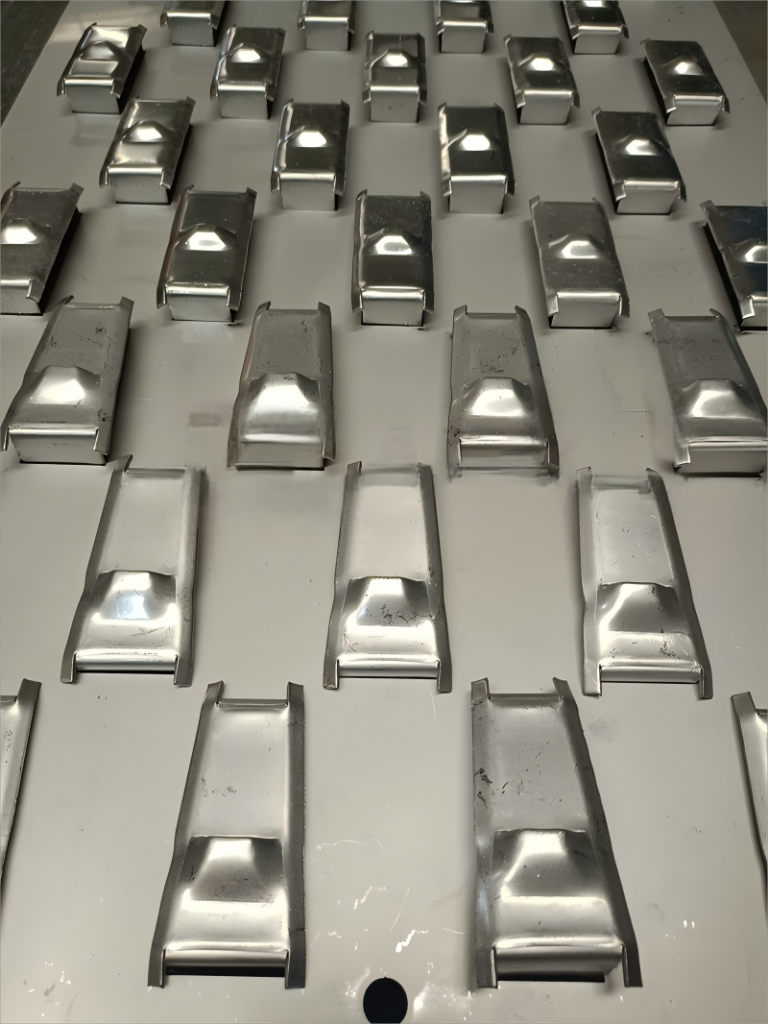
Product Features and Benefits
1.Disc float valve
Disc-shaped float valve tower plate also has its own shortcomings: ① between neighboring float valves, the horizontal blowing gas collision, resulting in increased entrainment of foam, and easy to lead to the return of liquid mixing on the tower plate; ② when the gas velocity is relatively large, the circular float valve is prone to rotate in the valve holes, friction caused by friction with the plate, so that the float valve is easy to wear and tear, off; ③ due to the edge of the tower plate can not be installed float valves, so easy to produce the edge of the tower plate dead zone of mass transfer ④ The tower plate is densely covered with raised floating valves, which will hinder the flow of materials on the tower plate when the materials are more viscous; ⑤ There is no bubbling area on the top of the valve cover, and the gas-liquid contact condition on the top is poor, which results in the lowering of the mass transfer efficiency of the tower plate.
2. Strip float valve
Strip float valve overcomes the shortcomings of disc-shaped float valve which is easy to rotate and easy to wear, but the gas-liquid collision between two neighboring valve bodies of strip float valve is more serious, and the liquid surface difference is large, which affects the processing capacity of the tower plate. Based on the P-type bar float valve and BDP-type bar float valve defects, the development of a variety of new types of float valve tower plate, such as L1 bar float valve tower plate, T-shaped arrangement of bar valve tower plate, HT Ⅴ ship-shaped float valve tower plate, BT Ⅴ float valve tower plate, guided float valve tower plate, a combination of guided float valve tower plate, high elasticity float valve tower plate, etc.
3.HTV ship-shaped float valve tower plate
Ship-shaped float valve, its valve parts and tower plate structure. As can be seen, HTV boat-shaped float valve will be ordinary bar float valve flat-top valve to have a concave semicircular and uniformly streamlined on both sides of the long bar valve, this setup ensures the smooth flow of the gas flow path, reduces the vortex generated by the flat-top float valve, to overcome the unstable state of the ordinary float valve. HTV valve parts in the tower plate with the long axis and the flow of parallel to the way of the way to arrange to reduce the axial return to the mixing, conducive to the mass transfer process. Favorable to the mass transfer.
4. Guided trapezoidal float valve
Guided trapezoidal float valve and F1-type float valve tower plate performance comparison has the following advantages: ① tower plate structure is simple; ② tower plate pressure drop can be reduced by 15% to 20%, the lower limit of the gas-phase load can be reduced by 1/3 or so, the upper limit of the gas-phase load can be increased by 10% to 20%, the operating flexibility is greatly improved. The guided floating valve tower plate has been used instead of F1 type floating valve tower plate in the normal decompression tower of oil refinery, de-benzene tower of gas plant and ethanol plant, and all of them have gained significant effect.
5.ADV Differential Float Valve
ADV float valve tower plate in the original F1 float valve tower plate to do some innovation, the main innovations are: ① in the top of the float valve valve to open a small valve hole, in order to promote the float valve above the liquid bubbles, increase the float valve above the gas-liquid contact; ② part of the ADV differential float valve has a certain guiding function to eliminate the difference in liquid level on the plate; ③ in the liquid drop tube area with upward protruding bubbles to promote; ④ on the drop tube and the float valve legs to improve the liquid. ADV floating valve tower plate has the advantages of high mass transfer efficiency and small liquid leakage, etc., and has been applied in industry.
6. Solid valve type tower plate
The solid valve and the tower plate are a single unit, whose shape can be made into square, round or other mature float valve structure. This approach is easy to process, reducing production costs, and performance between the float valve and screen plate. The gap between the bonnet and the legs is a gas flow path, and the gas flow does not need to support the floating bonnet, which has a lower pressure drop than the float plate. Relative to the screen plate, the gas flow is from the valve holes horizontally, which reduces the mist entrainment, therefore, the processing capacity is larger than the screen plate tower under the same opening ratio.V Its main features are: the surface of the floating valve is trapezoidal, and the gas flow direction and the liquid flow direction have a forward angle.
Product application industry
Petroleum refining and chemical industry
Application scenarios:
Crude oil atmospheric and vacuum distillation: separation of naphtha, diesel and wax oil in the primary distillation tower and atmospheric tower;
Catalytic cracking fractionation tower: separation of dry gas, liquefied gas, gasoline and recycled oil;
Ethylene cracking quenching tower: rapid cooling of cracked gas and heat recovery.
Natural gas processing
Typical processes:
Amine desulfurization and decarbonization: using MDEA solution to remove H₂S/CO₂ in the absorption tower;
Natural gas liquid (NGL) recovery: separating ethane, propane and butane through a distillation tower.
Environmental protection and waste gas treatment
VOCs recovery: Use special solvents (such as silicone oil) in the absorption tower to capture organic waste gas;
Acid mist treatment: Use alkaline solution to neutralize acidic gases such as HCl and SO₃.
Innovative application: Honeycomb floating valve tray, which improves mass transfer efficiency by 20% compared with traditional designs.
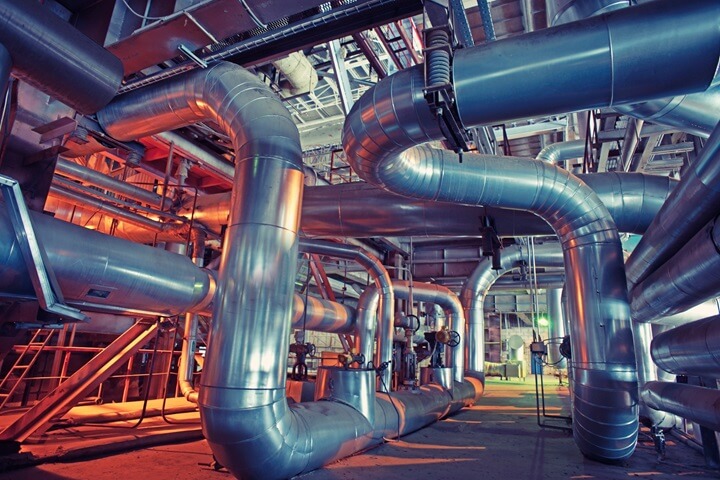
FAQ
When the medium has high viscosity or contains solid impurities, the liquid film will be deposited on the hinge. It is recommended to flush the valve shaft area regularly or use anti-stick coating.
The float valve needs to overcome the gravity of the valve plate and the shear force of the liquid film. Usually, the opening pressure is larger at low loads, which can be improved by reducing the valve plate size or optimizing the liquid flooding depth on the plate surface.
Choose corrosion-resistant materials (such as 316L, nickel alloy) or perform electrochemical passivation on the surface, check the valve hole edge regularly, and replace worn parts in time.
It is widely used in process towers that require precise gas-liquid contact, such as petrochemical, natural gas desulfurization, solvent recovery, fermentation distillation, and waste gas washing.
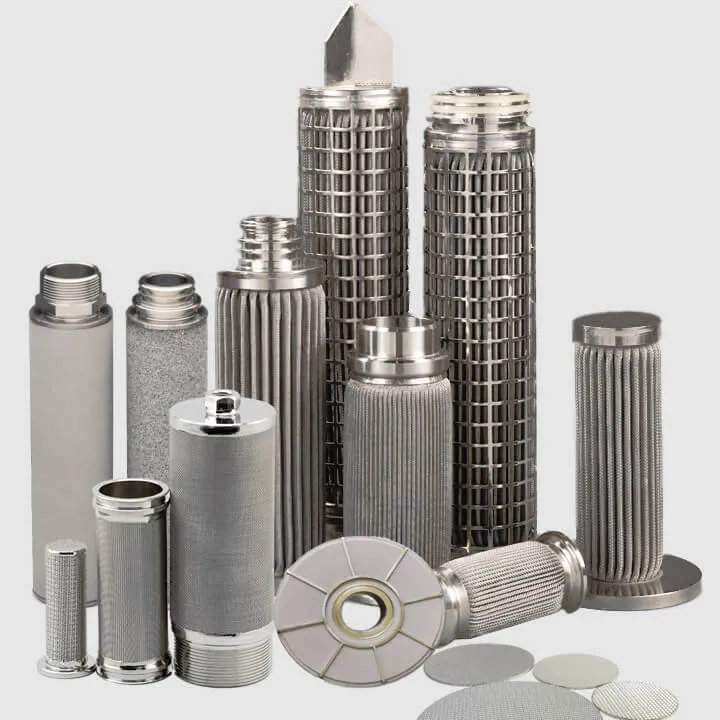
Sintered filter element

Mesh Demister

Wire Mesh Packing
